Novus Applications mejora el proceso del moldeo por inyección con la Rigid 10K Resin
El moldeo por inyección es un proceso de fabricación común y versátil que se usar para producir un volumen elevado de piezas. Mira a tu alrededor, ya que es probable que tengas cerca algo que se haya producido mediante moldeo por inyección: piezas y componentes de productos, embalajes y tapones de botellas, entre otras cosas. Muchos fabricantes recurren al moldeo por inyección para obtener piezas precisas y repetibles, usándolo en procesos de fabricación en sectores como la fabricación de electrodomésticos, la electrónica y la industria automovilística. La fabricación de moldes puede ser un proceso largo y costoso. Con costes iniciales elevados del equipo, mecanizar moldes puede resultar inconveniente. Sin embargo, existe alternativas a la mecanización de moldes en metal.
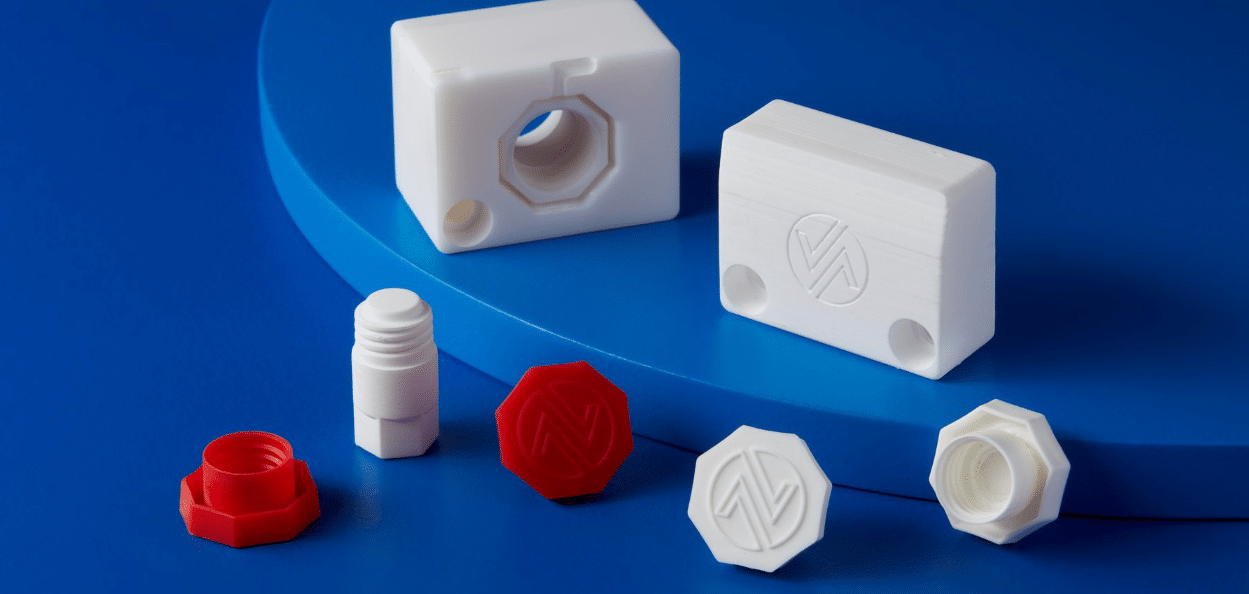
El trasfondo de Novus
Novus tiene un alcance amplio, ya que trabaja en los sectores de la asistencia médica personalizada, la asistencia en casa y la odontología, y colabora con algunas de las mayores marcas. Completa diseños para el fabricante, realiza estudios de moldeabilidad, realiza prototipos e iteraciones con rapidez, imprimen en 3D piezas y componentes y produceprototipos a pequeña escala para que los clientes puedan probar sus productos. Novus se centra en los plásticos moldeados por inyección y en el uso de estas piezas de plástico en ensamblajes de productos de consumo.
Hay una gran demanda de piezas moldeadas por inyección, que abarca desde empresas médicas a grandes marcas como Colgate y Liquiglide. Novus ha refinado su producción con años de experiencia.
“El moldeo por inyección es inherentemente exigente desde la perspectiva de la precisión y la de la experiencia. Para ser hábil al moldear por inyección, es necesario tener mucha experiencia en ello. Si se empieza a moldear sin mucha experiencia, hay mucho ensayo y error, frustraciones e incógnitas, a no ser que uno sepa qué es lo que se encuentra”.
Mark Bartlett, presidente y fundador de Novus.
“Del mismo modo, fabricar los moldes para el moldeo por inyección en el ámbito de la construcción de herramientas requiere un alto grado de precisión. Hay mucha experiencia que entender. ¿Cómo se resuelven los problemas antes de que ocurran? ¿Y qué hace falta para moldear la pieza sin rebaba, con un aspecto atractivo y cumpliendo de forma apropiada todos los requisitos del programa?”
Cómo aprovechar la impresión 3D en el proceso de trabajo del moldeo por inyección
Las fases iniciales del proceso de moldeo por inyección de Novus son las siguientes:
- Examina la pieza para comprender sus parámetros y cuál es el material más adecuado.
- Piensa en cómo inyectar y desoldar la pieza de forma que tenga un resultado preciso que
se corresponda con la forma deseada. - Renderiza el modelo de la pieza deseada en un software CAD.
- Construye modelos sólidos que representen diferentes piezas del molde.
- Decide cómo ensamblar el molde.
Con la impresión 3D, Novus puede prescindir del software de alta gama, con lo que ahorra tiempo por parte del usuario. Por consiguiente, el proceso está más automatizado. “La producción de estas piezas se realiza sin vigilancia. No necesito una persona con mucha experiencia, pero sí que necesito a alguien con experiencia en la impresión 3D. Así, la curva de aprendizaje es más rápida. La producción requiere mucha menos supervisión”, dijo Bartlett.
Bartlett añadió que le había impactado la simplicidad de la impresión 3D después de haber trabajado anteriormente en la fabricación de herramientas y en la programación de máquinas CNC. A Bartlett también le asombró lo asequible que era el conjunto. Dijo que las impresoras 3D de Formlabs entraban sin problemas en su presupuesto y que superaban a las máquinas de modelado por deposición fundida (FDM). Según él, Formlabs ofrece impresión de alta calidad a un coste bajo y con una amplia gama de materiales. “Mucha gente no entiende que sí que existe un término medio entre una impresora 3D de precio muy elevado y la versión de escritorio [de calidad] que se puede comprar para el hogar. Yo creía que ese término medio no existía en el mercado, por lo que Formlabs ha hecho un trabajo excelente… Ha sido capaz de ofrecer resultados de un nivel profesional”.
Por ejemplo, Novus produce muchas tapas y cierres. La empresa necesitaba producir una gran cantidad de series pequeñas de prototipos, de modo que requería un método rápido de producción. Según Bartlett, crear prototipos rápidos de una tapa en un molde impreso en 3D ayudó a agilizar su proceso de trabajo.
Cómo la Rigid 10K Resin permitió a Novus diseñar más rápido
Hay muchas formas de mejorar la impresión 3D y elegir el material adecuado es una de ellas. Bartlett buscó específicamente la Rigid 10K Resin porque quería estudiar la longevidad de un molde impreso y para ello necesitaba un material lo bastante rígido como para soportar la presión de este proceso, incluso con un diseño complejo. La tenacidad, la rigidez y la resistencia térmica de la Rigid 10K Resin la hacen ideal para fabricar moldes de moldeo por inyección en series cortas. Novus necesitaba producir rápidamente una gran cantidad de series pequeñas de prototipos. Las piezas de resina curada sirvieron como base en el moldeo por inyección para fabricar moldes sencillos a pequeña escala, que con el tiempo, evolucionaron hasta convertirse en piezas cada vez más complejas. “Cuanto más compleja se vuelve la tapa o el embalaje, más difícil es hacerlos con un conjunto de moldes impresos en 3D”, dijo Bartlett. “Queríamos explorar qué nos podía ofrecer la nueva resina con un alto nivel de relleno. ¿Qué era capaz de soportar? ¿Qué nos permitiría hacer?”
La precisión es esencial en el moldeo por inyección, con lo que la calidad de las piezas es crucial. “Necesitamos piezas que no solo puedan soportar temperaturas y presiones determinadas, sino que estén bien colocadas en el molde y no vayan a doblarse, derretirse o romperse. Y claro, necesitan poder soportar esas presiones. A continuación, durante el proceso de desmoldeo, tengo que poder ejercer fuerzas sobre esas mismas piezas que sacarán el plástico del molde sin destrozar las piezas impresas”, dijo Bartlett.
Novus eligió la Rigid 10K Resin porque combina una gran tenacidad, rigidez y resistencia térmica. Necesitaban un material capaz de soportar el gran calor y la gran presión de este proceso, plasmando al mismo tiempo detalles pequeños. Concretamente, el núcleo roscado era una pieza delicada. Gracias a este conjunto de propiedades, pudieron inyectar cientos de piezas de polipropileno y polietileno con un molde sin que se produzcan roturas.
La siguiente tabla muestra algunas de las condiciones de moldeo aplicadas a un único molde sin daños visibles. El molde mostró ciertos fallos a una presión de 11 500 psi.
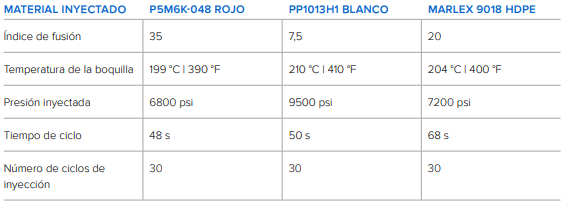
La siguiente tabla muestra mediciones sobre la pieza final inyectada en tres materiales distintos. En cada caso, el equipo midió 20 diámetros de las piezas roscadas para evaluar la repetibilidadde este proceso. Podemos observar una desviación media respecto al diámetro medio de ±0,04mm en esas 60 tapas, lo que refleja una buena estabilidad dimensional.
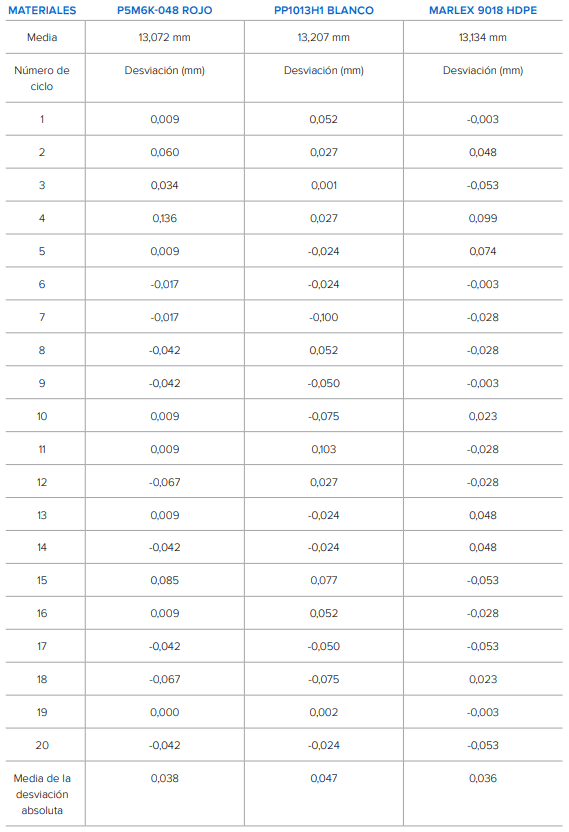
La Rigid 10K Resin no solo muestra una buena estabilidad dimensional, sino que también es más rápida y fácil de imprimir en comparación con el fresado del aluminio y el acero. “¿Qué comportamiento ha tenido la Rigid 10k Resin sometida a las presiones y las temperaturas de los materiales que utilizamos? Tuvo un rendimiento excelente… rendía a un nivel del que no considerábamos capaz al material tradicional [Rigid 400 Resin]”, dijo Bartlett.
Novus pasó por una iteración para llegar al diseño final y pudo ahorrar tiempo. “Puedo imprimir formas complejas con precisión, en mucho menos tiempo del que tardaría en fabricarlas de forma mecánica”, dijo. Aunque Bartlett no se esperaba conseguir piezas completamente perfectas, Novus no tuvo que ajustar las superficies de moldeo, solo refinó el exterior de los moldes múltiples. “Cuando llegamos hasta el molde, lo probamos. Después, inspeccionamos las piezas de plástico moldeadas y resultaron ser sorprendentemente precisas para no haber realizado iteraciones. Hicimos una impresión, una única serie, y el resultado fue magnífico”, dijo Bartlett.
Al ver las piezas repetibles con estabilidad dimensional que producía la Rigid 10K Resin, Bartlett dijo que la resina se convirtió en su elección para piezas pequeñas y complejas. “La hemos estado usando en otros componentes internos en los que la precisión y la estabilidad son imprescindibles”.