Guía de resolucion de problemas de impresion 3D
Esta guía constituye un excelente punto de partida si estás buscando mejorar la calidad de tus piezas impresas en 3D. Compilamos una lista extensiva (y en crecimiento) de las problemáticas más usualmente encontradas al momento de imprimir. Asimismo, presentamos las problemáticas con las posibles causas y soluciones para que puedas optimizar tus resultados de manera fácil y sencilla. En cada sección podrás encontrar imagines descriptivas para que identifiques rápidamente cada caso.
Vista en mosaicos de errores de impresión 3D
Utiliza la vista en mosaicos para identificar la imagen más representativa del defecto observado. Podes clickear en las imágenespara saltar directamente a cada sección de la lista de casos y obtener recomendaciones sobre cómo resolver el defecto de la mejor forma. Si no estás pudiendo encontrar un caso en particular sentite libre de leer en detalle los textos descriptivos. Hay múltiples consejos y sugerencias que pueden ayudarte a mejorar la calidad de tus impresiones.
Lista de casos de problemas comunes en impresión 3d
En la vista de lista cada defecto será descrito en detalle y se analizaran las posibles causas del problema así como una serie de instrucciones para resolver el inconveniente. Cada sugerencia particular se expresa como título. Si te interesa leer más sobre un caso en particular solo tenés que hacer click en el signo más (“+”) para expandir dicho bloque.
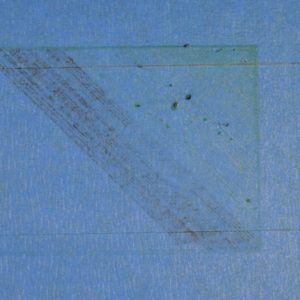
Al iniciar el trabajo la impresora no imprime
Si el fusor se halla excesivamente cerca de la superficie de impresión impedirá por completo la extrusión. Una forma de identificar esta situación es observar si el equipo no extruye material durante las primeras capas pero en capas subsiguientes opera de manera correcta. Para simplificar esto existen dos opciones, configurar el cero del programa en otra posición o recalibrar la plataforma de impresión. En caso de saber que la corrección necesaria es solo en el sentido del eje z se puede agregar un desplazamiento por programa. Por ejemplo, adicionar un valor de 0.05mm en el cero de z e ir incrementando dicho valor hasta observar que la primera capa se imprime adecuadamente.
La mayoría de las impresoras 3D usan un pequeño engranaje o buje moleteado para empujar el filamento hacia adentro o afuera del fusor. Los dientes de este engranaje o buje se hincan (muerden) el filamento y permiten controlar con precisión la posición del filamento. Sin embargo, si se observan muchas limaduras plásticas o se observa una sección faltante en el filamento es posible que el buje o engranaje este desbastando demasiado el plástico. En caso de que esto suceda el sistema no podrá traccionar el filamento. En estos casos refiérase a la sección de “Filamento Comido” para mayores indicaciones en cómo resolver este tema.
Si ninguna de las sugerencias anteriores logra solucionar este tema es probable que el extrusor este obturado. Esto puede suceder si alguna partícula externa de tamaño considerable queda atrapada dentro del fusor, cuando el plástico caliente se estaciona dentro del fusor durante periodos prolongados o si el sistema de enfriamiento del fusor no es suficiente y el filamento comienza a ablandarse por fuera de la zona específica para la fusión. La reparación de un extrusor obturado puede requerir el desmontaje del extrusor por lo cual tenga a consideración contactar al fabricante de su impresora antes de proceder. Nosotros hemos tenido buenos resultados utilizando unCalisuar de diámetro 0,35mm (objeto punzante utilizado usualmente para destapar picos de gas) mediante la introducción de dicha pieza por el orificio de salida del fusor.
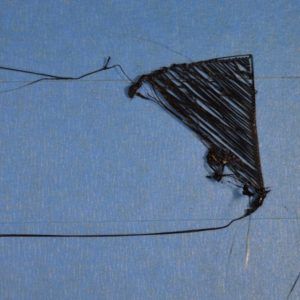
El material no se adhiere a la cama
El fusor comienza demasiado lejos de la cama
Una vez que la plataforma ha sido correctamente nivelada, aun es necesario verificar que el fusor comience a la distancia correcta de la plataforma – ni demasiado lejos ni demasiado cerca. Para una adhesión correcta a la plataforma se busca que el filamento este ligeramente comprimido contra la superficie. Mientras que estas condiciones pueden ser ajustadas por hardware, es mucho más sencillo y preciso realizar estos cambios por software
To do this, click “Edit Process Settings” to open your process settings and then go to the G-Code tab. You can use the Z-Axis global G-Code Offset to make very fine adjustments to your nozzle position. For example, if you enter -0.05mm for the Z-axis G-Code offset, the nozzle will begin printing 0.05mm closer to your build platform. Be careful to only make small adjustments to this setting. Each layer of your part is usually only around 0.2mm thick, so a small adjustment goes a long way!
Varias impresorasque están diseñadas para trabajar materiales de alta temperatura como el ABS incluyen una plataforma calefaccionada para reducir estos inconvenientes. Si la plataforma está configurada para mantener una temperatura de 100°C durante toda la impresión, esto colaborará con mantener la primera capa a temperatura evitando que se contraiga. Con lo cual si su impresora posee plataforma calefaccionada se puede probar calentar la cama para evitar que la primera cama se enfríe. Como un punto de partida, el PLA tiende a adherirse bien a una superficie entre 60 y 70°C mientras que el ABS opera mejor si la temperatura de la cama es de 100°C. Dependiendo del software es posible seleccionar diferentes temperaturas de cama para la primear capa y las restantes.
Si tu impresora posee un ventilador de enfriado, también se puede probar deshabilitar el mismo durante la impresión de las primeras capas para que no se enfríen de manera tan rápida. La posibilidad de modificar este parámetro también depende del software en cuestión. En general para la impresión de ABS es normal deshabilitar por completo el ventilador de enfriado. En caso de ambientes con corrientes de aire es importante cuidar de aislar el equipo para que las mismas no afecten el funcionamiento.
Por ejemplo, utilizar una BuildTak sobre la cama puede funcionar muy bien para PLA. Otros fabricante optan por una superficie calefaccionada de vidrio tratado por ejemplo con boro, el que tiende a funcionar muy bien con ABS. Si se planea imprimir directamente sobre estas superficies siempre es bueno asegurarse de que las mismas estén limpias de polvo, grasa o aceites. Para limpiar la plataforma sepuede utilizar un paño con agua o alcohol isopropilico.
Si su impresora no incluye materiales especiales asociados ala plataforma aun existen alternativas. Varios tipos de cinta se adhieren perfectamente a los materiales de impresión. Tiras de cinta pueden ser aplicadas a la superficie y luego removidas fácilmente si se desea imprimir con otro material. Por ejemplo, PLA tiende a adherirse bien a la cinta de pintor (azul) mientras que el ABS tiende a adherirse mejor a la cinta Kapton (tambien conocida como cinta de poliamida). Varios usuarios tambien han tenido buenos resultados utilizando adhesivos en barra o sprays liquidos sobre la plataforma. La laca de pelo utilizada en peluquerías es un excelente ejemplo.
Aveces se está imprimiendo una pieza pequeña que simplemente no tiene la suficiente superficie de contacto con la plataforma para adherirse de manera adecuada. La mayoría de los softwares de impresión incluyen opciones para aumentar la superficie del contacto. Una de estas opciones es llamada “BRIM”dd. El Brim o Voladizo agrega perímetros de material alrededor de la base del diseño original. Dependiendo de la morfología de la pieza en cuestión puede que sea necesarios brims entre 5 y 20 perímetros por lo cual aconsejamos realizar experiencias en cada caso particular. Otra alternativa es el uso del “RAFT” o Balsa.
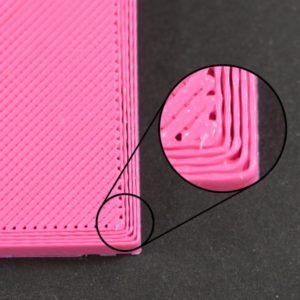
Extrusión insuficiente de material
El primer parámetro a verificar es el diámetro del filamento utilizado. El valor configurado en el programa debe ser acorde al material actualmente insertado en el fusor. Los valores usuales son 1.75mm o 3mm y en general las bobinas de filamento cuentan con algún tipo de etiqueta con el diámetro asociado. Igualmente, para mayor precisión se puede utilizar un calibre para tomar un número de muestras a lo largo de 1 metro de material y verificar que el diámetro sea acorde al utilizado en el programa.
Otros usuarios tal vez prefieren realizar una extrusión manual del filamento justo antes de imprimir.
SI el diámetro del filamento fue configurado correctamente y aun se observa sub-extrusión es recomendable ajustar la configuración del multiplicador de extrusión (extrusión multiplier, flow,etc). Dependiendo del software este valor es expresado como un coeficiente multiplicador o de forma porcentual. Por ejemplo, si originariamente el multiplicador fue configurado en 1.0 pruebe configurar el multiplicador en 1.05 para incrementar el caudal en 5% y verifique si los problemas de sub-extrusión desaparecen del cubo previamente analizado.
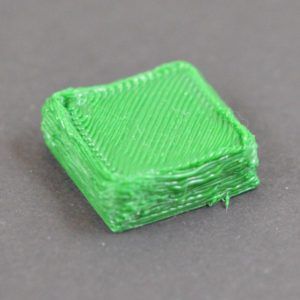
Extrusión excesiva de material

Huecos y espacios en capas superiores
El primer parámetro a modificar es la cantidad de capas solidas en laparte superior del modelo. Cuando se intentaimprimir una capa 100% sólida sobre el entramado parcialmente hueco, dicha capa debe extenderse sobre los huecos propios del entramado. Cuando esto sucede, la capa depositada tiende a deformarse en torno al entramado generando curvaturas o “bolsillos”. Debido a esto, para lograr una capa sólida con una buena terminaciónsuperficial puede que sea necesario el uso de múltiples capas solidas de manera consecutiva. Como criterio general, se busca que el espesor de la capa superior sea de al menos 0.5mm. Por ejemplo, en caso de estar utilizando una altura de capa de 0.25mm se requerirán cuanto menos 2 capas sólidas en la parte superior. Así también, en caso de estar utilizando una altura de capa de 0.1mm, es recomendable utilizar no menos de 5 capas sólidas.Sin embargo, si el defecto se presenta aun cuando se cumple el criterio mencionado es recomendable incrementar aún más la cantidad de capas sólidas. Tenga en cuenta que el número de capas sólidas no modifica las dimensiones del modelo a imprimir.
El entramado interno de la pieza actúa como estructura de soporte para las capas superiores. Dado que las capas sólidas en la parte superior del modelo se construirán sobre éste, si el porcentaje de relleno es bajo es probable que el sustento proveído resulte insuficiente y se observen huecos en la terminación final. Si ya incrementó la cantidad de capas sólidas y aún se observen huecos, es recomendable incrementar el porcentaje del relleno y observe si la terminación mejora. Por ejemplo, si el porcentaje de relleno actual es de 30%, pruebe utilizando un entramado al 50%.

Generación de Hilos (stringing o cowebs)
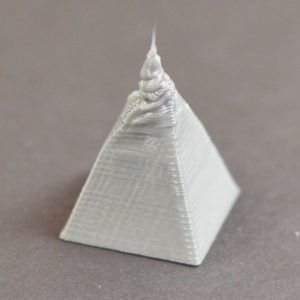
Temperatura excesiva
La causa más común para problemas por temperatura excesiva es que el plástico extruido no es enfriado lo suficientemente rápido. Cuando esto sucede el plástico continúa deformándose mientras se enfría. Para la mayoría de los materiales es mejor enfriar el mismo apenas se deposita para evitar que la capa cambie su forma una vez generada. Si el equipo incluye un ventilador de capa pruebe aumentar la velocidad del mismo. Si el equipo no cuenta con dicho ventilador se puede evaluar el montaje del mismo o utilizar un ventilador de mano.
Si ya intento con el ventilador de capa y aun se observan defectos se puede probar con disminuir la temperatura del fusor. Si el plástico es extruido a una temperatura menor será capaz de solidificarse más fácilmente. Pruebe disminuir la temperatura en 5 o 10 grados y verifique si los defectos disminuyen. Sin embargo, tenga cuidado de utilizar temperaturas demasiado bajas ya que podría impedir el proceso mismo de extrusión del material.
Si las capas se están imprimiendo a una velocidad excesiva puede que aun con un ventilador de capa el tiempo entre las mismas no sea suficiente para que el material se enfríe y solidifique de manera adecuada. Esto es particularmente importante para piezas pequeñas donde cada capa requiere solo segundos de impresión. Dependiendo del programa en cuestión se puede configurar un tiempo mínimo de capa, por ejemplo 15 segundos, y en caso de ser menor las velocidades se escalan para cumplir con dicho requisito. Este parámetro es crucial para evitar defectos por exceso de temperatura. Si considera que esto puede ser la causa de los defectos aumento el tiempo de capa y observe si la calidad mejora.

Desplazamiento de capas o desalineado
Si se está imprimiendo a una velocidad demasiado elevada puede que los motores se encuentren muy exigidos y en el caso extremo puede que supere el límite de capacidad de los mismos. Si esto sucede la sección restante del modelo presentará un desplazamiento respecto de la sección original. Si considera que la velocidad de impresión puede estar siendo excesiva intente reducir la misma en un 50% y observe si el desempeño mejora. Al configurar la velocidad es crucial reducir la velocidad de impresión así como también la velocidad de desplazamiento cuando el extrusor no se haya operativo ya que si cualquiera de las dos sobre exige a los motores puede generar un desplazamiento. Si posee experiencia con la configuración del programa tal vez tenga interés en reducir las aceleraciones máximas asociadas al firmware. De esta forma, se puede lograr que los cambios de velocidad resulten más graduales y el desempeño sea más óptimo.
Si el desplazamiento de capas continúa aun luego de reducir las velocidades, lo más probable es que se deba a cuestiones mecánicas o eléctricas. Por ejemplo, la mayoría de las impresoras 3D utilizan corras que permiten posicionar el extrusor. Con el tiempo las mismas pueden presentar cierta elongación, conllevando a una reducción en la tensión. Si esta tensión se reduce excesivamente puede que la correa resbale en la polea del motor y se pierda la referencia entre el giro del mismo y la posición del cabezal. Por el contrario, si la tensión con la cual fue instalada resulta excesiva la correa puede causar una fricción adicional en los rodamientos que en casos extremos podría impedir la rotación del motor. Un montaje ideal requiere que la correa este lo suficientemente tensa para prevenir la pérdida de pasos y evitar el deslizamiento pero no lo suficientemente tensa como para inmovilizar el rotor. Si se observan problemas de desplazamientos se recomienda verificar que las correas tengan la tensión adecuada. Si considera que el mecanismo presenta alguna complejidad adicional recomendamos ponerse en contacto con el fabricante del equipo para mayores instrucciones.
Muchas impresoras 3D incorporan una serie de correas que están accionadas mediante poleas dentadas. Dichas poleas se fijan al eje del motor mediante el uso de una chaveta o un prisionero (pequeño tornillo montado en la polea que ejerce presión radial sobre el eje del motor, en general sobre una sección rectificada del mismo). Si este tornillo esta flojo es probable que el eje del motor rote pero no así la polea ni el extrusor. Si el problema de desplazamiento de capas resulta recurrente es recomendable verificar que estos tornillos se hallen ajustados de manera adecuada.
También existen una serie de causas de tipo eléctrico relacionados con la perdida de referencia. Por ejemplo, si la corriente suministrada a los motores no resulta suficiente puede que los motores no puedan generar el torque esperado y en consecuencia no pueden efectuar la rotación solicitada. Así también, puede que la electrónica asociada al control de los motores se sobrecaliente. En estos casos un sistema de protección propio de la electrónica desactiva el motor transitoriamente hasta reducir la temperatura. Aunque esta no constituye una lista exhaustiva, provee una serie de ideas sobre algunos causantes del desplazamiento y su tratamiento.
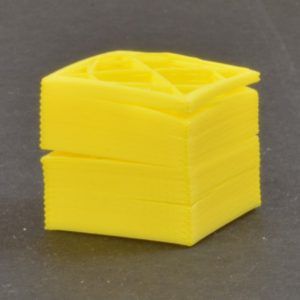
Separación de capas
La mayoría de los extrusores poseen orificios entre 0.3 y 0.5 mm. El plástico se extruye a través de este pequeño orificio para crear una fina capa.Sin embargo, las dimensiones de dicho orificio establecen limitaciones respecto del espesor mínimo que puede tener una capa. Durante el proceso de impresión se desea que una capa se imprima con cierta compresión sobre la previa para que ambas generen una unión consistente. Como criterio general, se debe verificar que la altura seleccionada sea un 20% menor al diámetro del fusor. Por ejemplo, si se trabaja con un fusor de 0.4mm, no es recomendable exceder una altura de capa de 0.32 mm o las capas no se podrán adherir. Si se observa que el modelo impreso presenta separación de capas el primer parámetro a verificar es que la altura de capa seleccionada sea acorde al diámetro del fusor. Intente reducir este parámetro y evalúe si la adherencia se incrementa.
La unión plástica es óptima si la capa previa y el material extruido se hallan cerca de la temperatura de extrusión. Si se presenta separación de capas y la altura de capa no es excesiva puede que la diferencia térmica entre el material extruido y la pieza deteriore la calidad de la unión. En principio esto se puede mejorar aumentando la temperatura de extrusión. Por ejemplo, si se intenta imprimir ABS a 200 grados se observará que las capas pueden ser separadas fácilmente. Esto se debe a que el ABS requiere una temperatura de 230 grados o más para crear una unión resistente. Si sospecha que esta puede ser la causa pruebe incrementar la temperatura en 10 grados y observe si mejora la Resistencia de las uniones. Por otra parte, si el tiempo de capa es elevado, ya sea porque la pieza posee un área grande o se están imprimiendo múltiples piezas en simultáneo, puede que la capa previa se enfríe excesivamente y deteriore la calidad de la unión. En caso de ser una pieza única las alternativas para evitar que la diferencia térmica sea elevada es incrementar la temperatura de la pieza mediante el aumento de la temperatura ambiente / plataforma ó reducir el tiempo de impresión por capa. En caso de estar imprimiendo múltiples piezas también se puede evaluar reducir el tiempo de capa mediante la reducción de la cantidad de piezas impresas de manera simultánea

Desgaste del filamento
Si aún se observa un desgaste del filamento, pruebe incrementar la temperatura del extrusor en 5 o 10 grados de forma que el plástico pueda fluir con mayor facilidad. Los plásticos en general presentan una viscosidad, y en consecuencia una resistencia, que decrece con la temperatura. Tenga en cuenta esto ya que puede resultar útil para evitar sub-extrusión en distintos materiales.
Si continua encontrando signos de desgaste enel filamento aun después de incrementar la temperatura, entonces el próximo parámetro que debería ser modificado es la velocidad de impresión. Si se reduce la velocidad el motor del extrusor no tendrá que rotar tan rápido y se evitará que la polea de empuje desbaste el filamento. Por ejemplo, si previamente se estaba imprimiendo a 60 mm/s pruebe reducir dicho valor en un 50% y observe si desaparece el inconveniente.

Extrusor Obturado

La extrusión se interrumpe durante la impresión
Esta causa es bastante obvia, pero antes de analizar las cuestiones restantes es importante verificar que aun exista filamento en la admisión del extrusor. Si la bobina se vació se debe reemplazar la misma por una que tenga material antes de continuar con la impresión.
Durante la impresión el motor de empuje tracciona el filamento hacia el interior del fusor. Si la velocidad de dicho motor es excesiva puede que en vez de traccionar el filamento se genere un desgaste del mismo. SI el desgaste es considerable puede que la reducción del material no permita traccionarlo. En dicha situación refiérase a la sección “Desgaste del filamento” para un análisis detallado de cómo tratar esta situación.
Si ninguna de las sugerencias previas aplica a su condición es probable que el fusor se encuentre obturado. Si esto sucede durante la impresión es recomendable realizar una inspección del material utilizado y chequear que el mismo no presente polvo u otra suciedad. Existen otras posibles causas para un bloque del extrusor, para un análisis detallado de las mismas refiérase a la sección “Al iniciar el trabajo la impresora no extruye – El extrusor esta obturado”.
Dado que el motor del extrusor se encuentra operativa durante gran parte del proceso y efectúa un trabajo elevado, es esperable que el consumo de corriente sea considerable. Si la electrónica de control de la impresora no cuenta con un sistema de refrigeración adecuado puede que el controlador del motor sobrecaliente. Estos controladores suelen contar con un sistema de protección por sobrecalentamiento y en caso de superar cierto umbral de seguridad, se desactivará el control del motor. SI esto sucede puede que los motores restantes continúen su operación pero el material no será extruido. La única forma de resolver esta cuestión es apagar el equipo y dar tiempo a que la electrónica se enfríe.Si el problema persiste otra posibilidad es agregar una fuente de refrigeración adicional o modificar la existente.
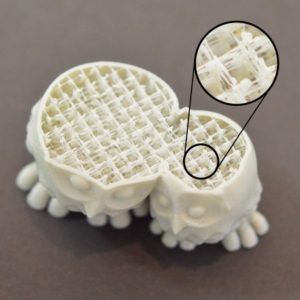
Relleno débil
Uno de los primero parámetros a evaluar consiste en el patrón del entramado. Dependiendo del programa en cuestión puede o no ser configurable. Algunos patrones suelen ser más sólidos que otros. Por ejemplo, los patrones de grilla, triangular y panal sólido (solidhoneycomb) son muy resistentes mientras que otros como el rectilíneo y panal rápido (fasthoneycomb) tal vez sacrifican resistencia en pos de aumentar la velocidad. Si usted está encontrando problemas en relación a la resistencia mecánica del entramado realice ensayos con patrones diferentes.
El entramado típicamente es impreso a una velocidad mayor que cualquier otra porción del modelo. Si se intenta imprimir el entramado con velocidades excesivamente elevadas el fusor no será capaz de mantener el caudal requerido. Este fenómeno se puede identificar como trazos débiles que tienden a hilos. Si ya ha probado diferentes patrones de entramado y continúa teniendo problemas con la resistencia mecánica del relleno, pruebe disminuir la velocidad de impresión asociada a los entramados. Por ejemplo, si se está utilizando una velocidad de 60 mm/s, pruebe con disminuir dicho valor en un 50% y verifique si el entramado mejora su calidad.
Otra posible modificación ofrecida por algunos programas es la modificación del grosor de extrusión de manera diferencial para los entramados del modelo. Por ejemplo, se podría utilizar un grosor de 0,4mm para los perímetros con una transición a 0.8mm para el entramado interno. Esto creará un entramado más grueso y firme mejorando notablemente la resistencia del modelo. En este sentido es importante tener en cuenta que al modificar el grosor de extrusión el programa busca mantener el porcentaje de relleno. Con lo cual, si se incrementa el grosor a un 200% el entramado utilizará el doble de material para cada trazo y para mantener el porcentaje de relleno el entramado tendrá un espaciado mayor. Por esta razón, muchos usuarios suelen incrementar el porcentaje de relleno en conjunto con el grosor de extrusión.
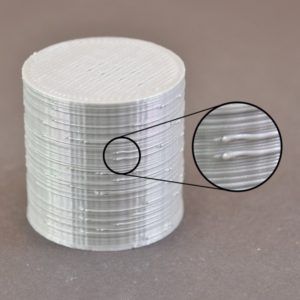
Manchas y granos
Si usted comienza a notar pequeños defectos en la superficie de la impresión, la mejor manera de diagnosticar su causa es observar como la impresión de cada perímetro del modelo. ¿El defecto aparece en el momento de la extrusora empieza a imprimir el perímetro? ¿O es que sólo aparece más tarde, cuando el perímetro se ha completado y la extrusora está llegando a una parada? Si el defecto aparece al inicio, es posible que sea necesario ajustar la configuración de retracción. Dependiendo del software puede que el mismo cuente con una configuración particular para modificar la retracción de manera diferencial para el caso de un cambio de capa. Este parámetro se puede encontrar como “distancia adicional de reinicio”, “Extra RestartDistance” u otras denominaciones. Para nuestro caso en cuestión, puede que el caudal extruido al comenzar el perímetro sea excesivo.Para reducirlo, se puede introducir un valor negativo en la distancia adicional de reinicio. Por ejemplo, si la distancia de retracción es de 1 mm y la distancia adicional de reinicio -0.2mm (nótese el signo negativo), cada vez que se detenga el extrusor, se efectúa una retracción de 1mm y al comenzar nuevamente solo se inyectará 0,8 mm de material. Ajuste esta configuración hasta que el defecto ya no aparezcaal inicio del perímetro.
Por otra parte, si el defecto se presenta al final del perímetro donde la extrusión se detiene el parámetro a configurar es otro. Dependiendo del software puede que la configuración del mismo sea o no posible. El mismo consiste en la interrupción de la extrusión antes de llegar al final del recorrido. Lo que se busca es y la detención de la extrusión liberando la presión generada dentro del fusor. Puede encontrarse como “Coasting” en la configuración de retracción. Habilite esta opción e incremente el valor hasta dejar de observar el defecto. Típicamente un valor entre 0.2 y 0.5 mm es suficiente para generar un cambio apreciable.
Los valores de “retracción adicional” y “coasting” mencionados anteriormente pueden ayudar a evitar defectos relacionados a la retracción de material, sin embargo, en algunos casos simplemente es mejor evitar las retracciones por completo. Esto es particularmente importante para las máquinas que utilizan una extrusora de tipo Bowden. Como se mencionó en la sección “Generación de hilos”, las retracciones se utilizan principalmente para evitar que la boquilla babeea medida que se desplaza entre las diferentes partes del modelo. Sin embargo, si la boquilla no cruza un espacio abierto, el babeo será interno e invisible desde el exterior. Por esta razón, muchos programas ofrecen una opción de “Sólo retraer al cruzar espacios abiertos” permitiendo así evitar retracciones innecesarias.
Asimismo, si la impresora realizará retracciones únicamente cuando se desplaza sobre espacios abiertos, sería interesante que el fusor evitara dichos espacios en cuanto sea posible. Si el extrusor puede evitar atravesar el perímetro mediante la modificación de su trayectoria, entonces la retracción no será necesaria. Algunos programas permiten configurar dicho comportamiento. En estos casos, para utilizar dicha configuración simplemente habilite la opción de “Evitar perímetros externos durante desplazamientos” /“Avoidcrossingoutlinefortravelmovement”.
Si aún se observan pequeños defectos superficiales, la mayoría de los softwares de impresión proveen una configuración opcional para modificar la ubicación de los puntos de partida. En general la ubicación de estos puntos es seleccionada con el objeto de optimizar la velocidad de impresión. Sin embargo, mediante el software también se puede posicionar los mismos de manera aleatoria o alinear los mismos en el plano XY (lo cual produce un efecto de cicatriz en eje Z). Por ejemplo, si se está imprimiendo una estatua, usted puede alinear todos los puntos de inicio en la parte posterior del modelo para que no sean visibles desde el frente.

Espacios entre relleno y perímetros
Dependiendo del software utilizado es posible aumentar la resistencia mecánica de la unión perímetro-relleno mediante el control del porcentaje de solapamiento entre ambos. Dicho parámetro suele denominarse “solapamiento” u “Overlap”. El mismo se expresa como un porcentaje del grosor de extrusión. Si se utiliza un solapamiento del 20% esto significa que el software indicará a la impresora que solape el relleno con el perímetro interior en un 20%. Este solapamiento garantiza una unión resistente entre ambas secciones. Por ejemplo, si se estaba utilizando un solapamiento del 20% y se observaban huecos se puede experimentar con un aumento al 30% y observar si los huecos desaparecen.
El relleno del modelo suele tener una velocidad de impresión mucho mayor que los perímetros. Sin embargo, si la velocidad es excesivamente alta el relleno no tendrá tiempo de adherirse al perímetro. Si ya intento incrementar el porcentaje de solapamiento pero aún se observan huecos entre los perímetros y el entramado interno es recomendable repetir el ensayo con una velocidad de impresión más baja. Por ejemplo, si previamente se imprimió a 60 mm/s intente reducir en un 50% la velocidad. Si efectivamente los huecos desaparecen, incremente la velocidad de manera gradual hasta encontrar la mayor configuración para la impresora.

Rizado en bordes duros / rectos

Cicatrices y terminación superficial
La primera cuestión a verificar es que no se esté extruyendo demasiado material. En este caso cada capa será ligeramente más espesa de lo esperado. Debido a esto, cuando el fusor se desplace sobre la pieza puede que arrastre parte de este plástico excesivo. Antes de analizar otras causas debe descartarse esta condición. Refiérase a la sección “Extrusión excesiva de material” para más detalles.
La primera cuestión a verificar es que no se esté extruyendo demasiado material. En este caso cada capa será ligeramente más espesa de lo esperado. Debido a esto, cuando el fusor se desplace sobre la pieza puede que arrastre parte de este plástico excesivo. Antes de analizar otras causas debe descartarse esta condición. Refiérase a la sección “Extrusión excesiva de material” para más detalles.
Si ya se aseguró de estar extruyendo la cantidad adecuada de material y aun se observan defectos por el desplazamiento del fusor sobre el material, puede resultar útil analizar la configuración de elevación vertical en el software. Esta opción permite configurar un desplazamiento vertical del fusor para las traslaciones sin extrusión. Mediante esto se puede evitar que el fusor marque la capa previamente impresa. Dependiendo del software, puede que este desplazamiento solo se habilite si se efectúa una retracción de material, también efectuada de manera previa al desplazamiento sin extrusión.

Huecos y espacios en ángulos contra el suelo
El agregado de perímetros adicionales aumentará considerablemente la resistencia de la estructura de la capa inferior. Dado que el interior de la pieza es parcialmente hueco, el grosor del perímetro tiene un efecto significante sobre la calidad de los cimientos para la capa subsiguiente. Por ejemplo, si previamente se imprimía con dos perímetros, repita el modelo utilizando cuatro perímetros para verificar si los huecos desaparecen.
Otra causa posible de cimientos débiles es la falta de suficientes capas sólidas en la parte superior. Dado que la primera capa solida se apoya en el entramado interno puede que la misma presente defectos y se requiera un cierto número de capas para lograr una capa sólida consistente que permita una correcta impresión. Si se estaban utilizando solo dos capas solidas intente imprimir el mismo diseño utilizando 4 capas sólidas para verificar si las bases mejoran.
El último parámetro a analizar es el porcentaje de relleno. Como se mencionó en la sección anterior, dependiendo del porcentaje de relleno es posible que se requiera un número mayor de capas sólidas para lograr una superficie de impresión consistente para la siguiente capa. Si el entramado es demasiado débil y el aumento de capas sólidas no alcanza para mejorar la terminación ó se desea mejorar la calidad sin modificar el número de capas sólidas se puede aumentar el porcentaje de relleno. Por ejemplo, si se está imprimiendo con un relleno de 20% pruebe utilizar un relleno de 40% y verifique si los huecos desaparecen.
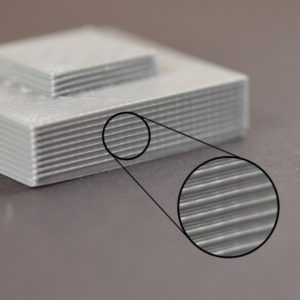
Lineas sobre los laterales
La causa más usual suele deberse a material de baja calidad. Si las tolerancias de fabricación del filamento son bajas la variación en el diámetro del mismo se traducirá en un caudal variable lo cual a su vez generará impresión de mayor grosor y en consecuencia en un efecto de líneas sobre las paredes. Para generar una pared lisa la impresora requiere un caudal constante y filamento de alta calidad. Para otras posibles causas de la variación en el grosor de extrusión por favor refiérase a la sección de Extrusión Inconstante.
La mayoría de las impresoras 3D utilizan un controlador PID para regular la temperatura del fusor. Si este no se configuró de manera adecuada la temperatura del fusor puede presentar oscilaciones amplias a lo largo del tiempo. Debido a la naturaleza propia de estos controladores esta fluctuación es cíclica. Con el cambio de temperatura el plástico cambiará sus propiedades (viscosidad) y fluirá de distintas formas. Esto conllevará a que distintas capas de la pieza se impriman de diferentes formas creando trazos visibles sobre el lateral. Un controlador correctamente configurado debería ser capaz de mantener la temperatura del extrusor acotada en +/- 2 grados. Si se observa que la temperatura presenta fluctuaciones mayores es probable que sea necesario recalibrar el controlador PID. Consulte el fabricante del equipo para las instrucciones respecto a la calibración del controlador.
Si se determina que la extrusión inconsistente y la variación térmica no son responsables de los defectos puede que exista alguna cuestión mecánica que esté generando el patrón de líneas en los costados del modelo impreso. Por ejemplo, si la plataforma de impresión presenta oscilaciones o vibraciones durante el proceso de extrusión es probable que cause variaciones en la posición del fusor en el eje z. En consecuencia, el espesor de algunas capas será ligeramente mayor al de otras. Otra causa común es el posicionamiento incorrecto de la varilla roscada del eje z. Por ejemplo, debido a problemas de backlash (juego) o una configuración incorrecta del controlador del motor. Pequeños cambios en la posición de la superficie pueden generar cambios significativos en la calidad de cada capa impresa. En este sentido recomendamos analizar las fuentes mencionadas y consultar con el fabricante del equipo si se observan anomalías notorias.

Vibraciones sobre laterales
La causa más usual suele ser una velocidad de desplazamiento excesiva. Cuando el extrusor de la impresora realiza cambios abruptos de dirección estos movimientos generan fuerzas adicionales que pueden conllevar a la generación de vibraciones estructurales. Si se sospecha que la impresora se puede estar desplazando demasiado rápido evalúe disminuir la velocidad. En la mayoría de los softwares se diferencia la velocidad durante una extrusión activa frente a la velocidad de desplazamiento sin extrusión. Para observar un cambio significativo se deben disminuir ambas velocidades.
El firmware de su impresora (software residente que controla los procesos mediante el comando de los motores y monitoreo de los sensores) típicamente implementa un control de la aceleración para evitar cambios bruscos en la dirección de desplazamiento. Esta configuración permite que ante un cambio la velocidad crezca y decrezca de manera controlada evitando la generación de vibraciones. Consulte con el fabricante de su equipo respecto de la configuración de este parámetro y en caso de ser posible experimente disminuyendo la aceleración para reducir las vibraciones.
Si con las sugerencias previas no se pudo resolver el defecto quizás sea recomendable analizar aquellas cuestiones mecánicas que estén generando vibraciones excesivas. Por ejemplo, puede que haya algún tornillo flojo o una fijación inadecuada que permiten la generación de dichas vibraciones. Observe su equipo de cerca mientras opera e intente identificar la fuente de las vibraciones.

Huecos en paredes delgadas
Si el espacio entre los perímetros es demasiado reducido puede que el programa no evalúe la generación de entramado interno para dicha sección. En estos casos algunos programas traen configuraciones adicionales. Por ejemplo, el Simplify3D tiene una opción de ”Relleno de huecos en caso de ser necesario/ Allow gap fillwhennecessary”. Por otra parte, si aún se observan huecos en el modelo es sugerible incrementar el porcentaje de solapamiento entre perímetro y entramado. Esto aumentará el área asociada al entramado y tal vez con dicha modificación el programa determine necesaria la generación de material de relleno. Si previamente se utilizaba un solapamiento del 20% repita el modelo incrementado el solapamiento a 30% y observe si la terminación de las paredes mejora.
En algunos casos puede resultar más eficaz efectuar una modificación en el grosor de la extrusión. Por ejemplo, si se está imprimiendo una pared de espesor 1mm, se recomienda utilizar un grosor de extrusión de 0.5mm para obtener un resultado rápido y resistente. Esto resulta eficiente para piezas cuyas paredes poseen un espesor relativamente constante.

No se imprimen algunos detalles pequeños
La primera y más obvia de las soluciones es rediseñar la pieza para que la misma cuente solo con características que sean más gruesas que el orificio del fusor. Típicamente esto conlleva a la modificación del archivo en el software de diseño original. Una vez que haya ensanchado los detalles pequeños se puede reimportar el diseño en el software de impresión para verificar que el mismo sea capaz de reproducir todas las características. Si las mismas son observables en la vista previa, entonces deberían ser generables en el modelo real.
En algunos casos la modificación del diseño no es una alternativa, ya sea por la funcionalidad del objeto en cuestión o porque dicho archivo esta bajado de internet y no se posee el editable. En tales circunstancias se puede evaluar la adquisición de un pico de menor diámetro que permita la impresión de detalles más pequeños. La mayoría de las impresoras tienen un pico removible lo cual hace el reemplazo bastante sencillo. Consulte con el fabricante de su equipo por las instrucciones exactas para instalar un pico de menor diámetro.

Extrusión Inconstante
En primer lugar se debe verificar la bobina de plástico que alimenta al equipo. Es importante asegurarse que la bobina pueda rotar libremente y que el plástico pueda ser des-bobinado sin grandes esfuerzos. Si el filamento se enreda o la bobina presenta un rozamiento excesivo en su rotación se alterará la calidad del material extruido y el diámetro será inconstante (o nulo).
Por otra parte, si la impresora presenta una guía de Bowden (pequeño tubo que guía al filamento desde el motor de empuje hasta el fusor),también se debe verificar que el filamento pueda deslizarse libremente por el mismo sin bloqueos ni grandes resistencias. Si se observa demasiada resistencia se puede evaluar limpiar el tubo o lubricar el mismo. Tener especial consideración al trabajar con materiales flexibles. Dependiendo de la rugosidad superficial del mismo el rozamiento entre la vaina del Bowden y el filamento podría bloquear el desplazamiento del mismo.
Si se observa extrusión inconsistente pero el filamento no está enredado y puede ser traccionado libremente hacia el extrusor el siguiente paso es corroborar el extrusor en sí. Es posible que alguna suciedad o partícula se haya ubicado dentro del fusor evitando la extrusión. Una manera de verificar esto es girar el motor de empuje o empujar el plástico hacia el fusor de manera manual verificando que el mismo salga de manera constante por el orificio de salida (que no debe estar bloqueado por la plataforma de impresión u otra cosa). Si se observan inconvenientes en dicho proceso es probable que sea necesario limpiar el fusor. Consulte con el fabricante del equipo respecto de las instrucciones para limpiar de manera adecuada el interior de su fusor.
Si la bobina de filamento gira libremente y el extrusor no se halla obturado puede resultar útil chequear la configuración del software. Por ejemplo, si se intenta imprimir con capas demasiado delgadas (0.01mm)el plástico tendrá poco espacio para salir del orificio del fusor y la resistencia generada al flujo será elevada. Chequee nuevamente para asegurarse de estar utilizando una altura de capa razonable. Pruebe utilizar un valor mayor y observar si el problema desaparece.
Otra configuración a analizar en el software es el grosor de extrusión especificado en el software. Dependiendo del software particular puede que la configuración se pueda realizar por cada extrusor particular. Como regla general, el grosor de extrusión debe estar entre el 100y el 150% del diámetro del orificio de salida. Si el grosor se halla por debajo del diámetro del fusorel extrusor será incapaz de extruir un caudal constante y se observarán defectos.
Una de las principales causas de una extrusión inconstante que aún no hemos mencionado es la calidad del filamento utilizado. Filamentos de baja calidad pueden contener aditivos que impactan en la consistencia del plástico y/o un diámetro de fabricación poco preciso el cual repercute directamente en el caudal generado. De manera adicional, varios plásticos tienden a degradarse con el tiempo. Por ejemplo, el PLA tiende a absorber humedad del aire y luego generar imperfecciones en la extrusión. A esto se debe que la mayoría de las bobinas de plásticos incluyan un disecante de silica gel en el empaquetado. Si considera que su filamento puede estar deteriorado, intente reemplazar el mismo por uno nuevo sellado y de alta calidad para corroborar si el inconveniente desaparece.
halla por debajo del diámetro del fusorel extrusor será incapaz de extruir un caudal constante y se observarán defectos.
Si chequeó todo lo anterior y aun continua teniendo problemas tal vez convenga evaluar la mecánica del extrusor. Muchos extrusores utilizan un sistema de poleas con dientes o hendiduras afiladas que traccionan el filamento. Estos extrusores suelen contar con un ajuste de la presión ejercida contra el filamento. Si la presión es demasiado débil la polea no podrá traccionar el material de manera adecuada y puede que el caudal generado no sea constante. Consulte con el fabricante de la impresora para saber si el equipo posee un ajuste similar.